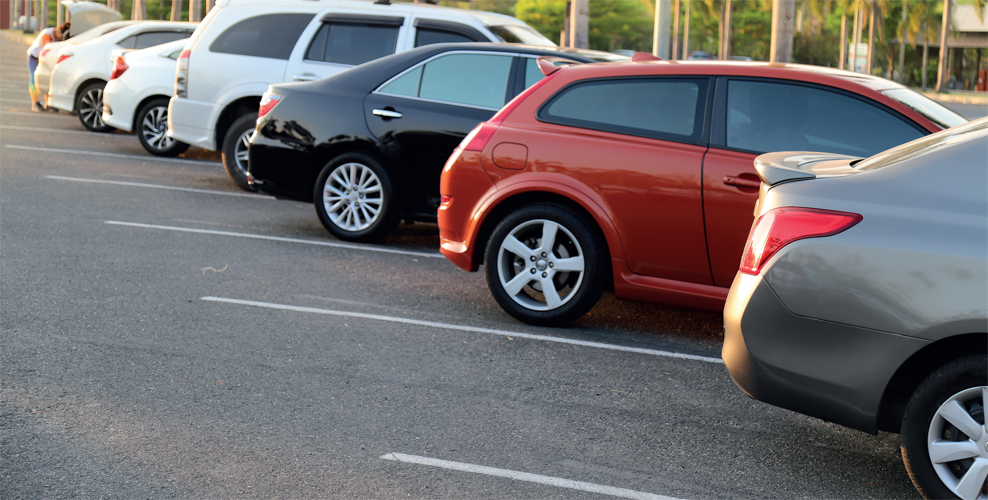
Smooth solutions
When should you conduct a parking lot condition survey? Emily Newton reports
Minor parking lot repairs — like crack sealing or patching — can significantly extend a lot’s lifespan and reduce repair costs down the line. However, small unaddressed issues can quickly become much more severe problems.
A parking lot survey can help you spot parking lot distress that you may be able to patch with the right maintenance. However, asphalt takes time to wear down, and it’s not practical to continually reevaluate your lot’s condition. Instead, you’ll need to develop a schedule of parking lot condition surveys.
Best practices for timing pavement surveys
A quality parking lot can last as long as 20 years before needing repaving. Between construction and then, however, the parking lot will need regular maintenance.
Typically, if a parking lot’s construction includes sealcoating, you’ll begin to see cracks appear about three to five years into its lifespan. These cracks can quickly expand, potentially growing into potholes. However, with the right treatment — crack sealers, fillers and other preservation methods1, like fog coatings — you can quickly manage them.
However, you’ll only know these cracks have emerged if someone’s keeping an eye on the parking lot, or if you’re regularly surveying your lot’s condition.
There’s no industry-standard metric for determining when it’s time to inspect parking lots, but you can borrow best practices and work backward from recommendations on lot maintenance to roughly estimate how frequently you should examine a lot.
Most state departments of transportation, for example, use a ride quality metric — like the International Roughness Index — to determine when pavement needs assessment or maintenance. If a ride across a stretch of pavement is sufficiently bumpy, the department will survey the road and begin to plan maintenance operations.
You can also base your frequency on how often parking lots need maintenance.
Recommendations vary somewhat on how frequently you should perform parking lot repairs. Some asphalt preservation experts recommend crack filling and sealcoating every three to five years, while others may advocate for more frequent sealcoating and less frequent filling.
If you haven’t inspected or maintained a parking lot in the last three to five years2, a condition survey will likely turn up some pavement distress you need to manage.
However, if there are signs of visible distress, you may want to stage a survey anyway, even if only a year or two has passed since the last examination.
Signs a pavement survey may be necessary
You may also want to adjust your surveying schedule based on your parking lot’s status. If there’s visible distress or major changes to the pavement since the last survey, it may be a good idea to stage an early condition survey. Catastrophic problems or design oversights can cause a parking lot to develop cracks or other damage ahead of schedule — meaning it can be valuable to inspect your lot before that three- to five-year milestone has passed.
It’s a good idea to familiarize yourself with the signs of visible pavement distress, like those outlined by the Federal Highway Administration Program’s classification system:
- Cracking
- Potholes
- Patches and patch deterioration
- Rutting
- Shoving
- Bleeding
- Polished aggregate
- Raveling
If you can see obvious or extensive damage to the parking lot at a glance — or if the pavement ride is rough or bumpy — it’s typically a good idea to stage an early condition survey.
If you already plan to spot-patch an area of a parking lot or fill a crack, it can also be a good idea to conduct a survey anyway. Condition surveys can reveal major structural or design defects, helping you identify root causes behind unusual or unexpected distress.
How to conduct a parking lot condition survey
Construction companies use a few different standard methods and metrics to survey asphalt parking lots’ condition. Some construction companies use the Pavement Surface Evaluation and Rating (or PASER) method3, which state transportation departments initially developed. The PASER method lends itself to a quick parking lot inspection. You won’t need to note every instance of distress, just the general condition of the lot.
At the end of your survey, you’ll be able to assign your parking lot a rating between one and ten. Lower ratings require more intensive repairs, while higher ratings may require little or no maintenance.
There are also more comprehensive standards available. The ASTM D6433-20, or Standard Practice for Roads and Parking Lots Pavement Condition Index Surveys, is the 2020 version of the American Society for Testing and Materials standard. The ASTM D6433-20 is likely the most in-depth standard available for parking lot surveys. With the standard, you’ll need to note every deformation, crack or patch on your parking lot, and record this distress in several ways.
Once the survey is complete, you’ll be able to calculate the pavement condition index for your lot, a number between 0 and 100 that represents how distressed the pavement is.
A survey that meets the ASTM D6433-20 standard will take significant time to complete. However, it will also provide you the best idea of your parking lot’s condition.
If the distress only consists of a few individual cracks or patches, the simpler PASER approach should work well. For more extensive damage, however, you may want the detail and specificity the ASTM’s standard provides. No matter what standard or practice you use to survey your lot, you should include the date of the inspection, as well as a future date for the next examination.
Know when to survey and repair a parking lot
Pavement surveys and maintenance can help ensure a parking lot lasts its full potential lifespan. In general, it’s good practice to survey frequently enough to catch new distress. A survey every three to five years, with additional surveys as needed, could be enough to help you identify common issues and prevent them from developing into major problems.
1 http://asphaltmagazine.com/the-importance-of-preserving-pavements/
2 https://www.dbkrieginc.com/parking-lot-maintenance.php
3 http://www.apa-mi.org/docs/Asphalt-PASERManual.pdf
Emily Newton is the Editor-in-Chief of Revolutionized, an online magazine exploring innovations in construction and industry. Subscribe or follow her on LinkedIn for more of her articles.
https://revolutionized.com/author/emily/