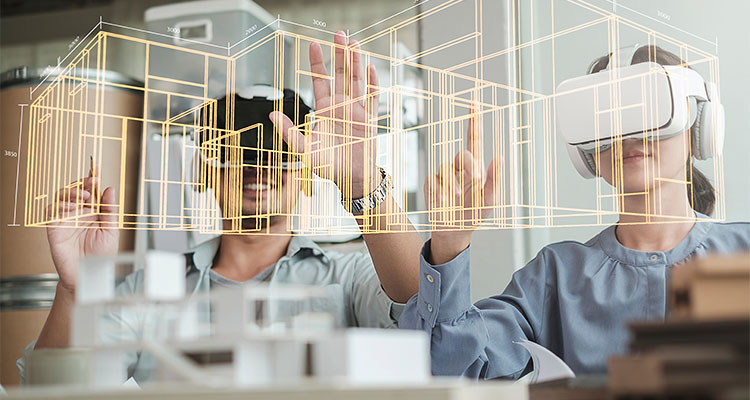
Boosting construction productivity with digital twins and augmented reality
As digital methods continue to revolutionize construction, the industry is going far beyond staples like Building Information Modeling (BIM). Increasingly advanced solutions like digital twins and Augmented Reality (AR) are finding a home on modern construction sites, dovetailing with solutions such as advanced sensor and data-harnessing technologies. These developments are changing the game for tech-savvy firms operating at the forefront of the sector, by offering greater efficiency and a route to error-free building.
Crews on the ground can use these powerful technologies to see clearly into the future, helping to maximize productivity, reduce waste, bring down project costs and eliminate project delays.
What is a digital twin?
While the technology underpinning them may be complex, digital twins are simply virtual replicas or representations of physical objects, processes, or systems. They can be created by combining real-time data from sensors, Internet of Things (IoT) devices that connect to wireless networks and transmit data, and other sources with advanced modeling and simulation techniques.
While identical in appearance, digital twins are smarter than their physical counterparts, distinguished by their capacity to be molded and analyzed with the click of a button. The ability to carry out simulations and highly accurate monitoring opens up a world of opportunity throughout all construction phases. Physical structures can be monitored, analyzed, and optimized by toying with their digital replicas, providing invaluable insights that inform predictive decision-making.
More than just a copy: smart design and planning
For instance, digital twins can be used during the design phase to create a virtual model of a construction project. Architects and engineers can visualize a structure and assess its feasibility, functionality, and aesthetics before a single brick is laid. They can also simulate different design options and evaluate their performance before construction begins.
Digital twins also shine in the planning stage, where they can be used to simulate activities, identify potential clashes or bottlenecks, and ultimately optimize workflows. This means crews can proactively assess the impact of different strategies, materials, or equipment on project timelines, as well as predict costs before potentially wasting resources.
Power in the data
As projects progress, digital twins can be used to monitor construction sites in real time using IoT sensors and other data collection devices and software. This can be through something as simple as a data collection form filled in by workers or more complex sensors in machinery. Cloud applications are pivotal to organizing and sharing this data collected on the ground.
To put the term data into context, digital information can cover various parameters such as temperature, humidity, structural integrity, and worker activities to provide a deeper understanding of how structures and crews are performing. This information is used to detect issues, ensure safety, and make informed decisions about construction processes.
Meanwhile, data on equipment collected from sensors can be used to monitor equipment performance, flagging anomalies to help workers predict and prevent maintenance issues to keep projects running smoothly.
Taking models off the screen
Similar in principle, AR brings 3D digital design models to life and allows workers to visualize them as holograms in the field. With the power of AR, teams can accurately compare holograms of BIM models against real structures to ensure they are built within tolerances – to millimeter accuracy using the most advanced tools – preventing design errors that lead to costly, reactive rework. Recent research in the Engineering Journal estimates rework can cost over 12 percent of project contract value – a value that cannot be ignored in such a challenging market.
Rework also has an inflationary effect on material waste. Material availability is still under pressure from supply chain challenges, high demand and logistical issues. A global shortage of cement, in particular, threatens projects while contractors are footing the bill from spiking energy costs and green compliance. In fact, commercial construction materials are 38 percent more expensive than at the start of 2022. Meanwhile, an almost five percent increase in overall construction input prices in the past year has been identified by the Associated Builders and Contractors Association.
A thing of the past
Paper designs and scribbled notes could and should be a thing of the past. As the industry moves away from reactive monitoring and rework, cutting-edge technologies like digital twins and AR are taking human error out of the picture, creating a new standard of work by facilitating greater accuracy and agility onsite. It’s now about removing the roadblocks for tech adoption in construction by showcasing the value
of innovations like these and the potential returns. Digital tech is opening the doors to a new era of technical empowerment and will break through the stagnation of the construction industry, if we allow it.
For a list of the sources used in this article, please contact the editor.
David Mitchell
www.xyzreality.com
David Mitchell is the Founder & CEO of construction technology company, XYZ Reality: the company behind the Atom – the world’s most accurate Engineering Grade Augmented Reality (AR) headset. Before founding XYZ Reality, David worked as a digital construction manager on some of Europe’s largest projects including: The Shard, Battersea power station and hyper-scale data centers. David is a leading expert in digital construction and has been recognized for his innovation in this space.